Wyler Zerotronic Sensors Delivers Wafers Faster
Precise determination
of inclinations is a critical requirement for Seagate Inc. (Bloomington,
MN), a vertically integrated builder of hard disk and tape drives
for data storage.
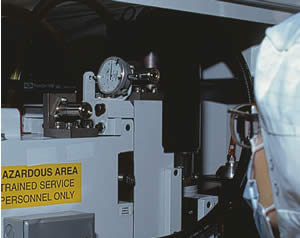 |
Mounted
on this grinder spindle, the
Wyler sensor system has helped Seagate Inc. increase the efficiency
of its wafer
grinding operations.
|
An outside vendor manufactures
wafer substrates by a unique hot-pressing process and then supplies
them to Seagate, which builds up its recording head structures on
them. Seagate's own ceramic-grinding operation on the finished wafer
is extremely sensitive. The 4.5-inch square wafers each worth thousands
of dollars are ground down to 1,250 microns. If the sensitive wafer
grinder used in the process is not set at precisely the required
angle, the work becomes too costly, and time-consuming adjustments
are required. This might take as many as 3 hours. Also, the labor
costs for highly trained technicians becomes unsupportable.
Seagate's technology
produces a variety of hardware and provides business intelligence,
and storage and network management services. But, at the heart of
its activities is the ability to make zero-defect recording heads
assembled at plants in various domestic and overseas locations.
When the company purchased
Fred V. Fowler Company's (Newton, MA) new Wyler Zerotronic sensor
system, it substantially increased the efficiency of its tightly
controlled and fine-tolerance processing operations. This digitized
inclination sensor fulfills the critical function of accurately
measuring the relative angle between the chuck holding the wafer
and the grind wheel axis.
"The spindle angle",
said Mike Kwilinski, a manufacturing engineer at Seagate, "is
important because of the type of grinding used to produce the wafers.
We must use a minimum spindle angle that best complements the hardness
of the self-dressing grinding wheel. One of the keys in setting
up the grinders is to measure a precise angle between the grind
spindle and the work chuck."
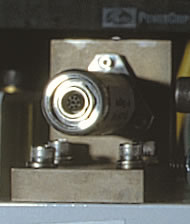 |
Closeup
of the Zerotronic Mounting. Cable has been removed for clarity. |
If the spindle angle
is too small, the wheels won't break down and will dull. When a
60-pound force on the machine is reached, the grinder stops and
manual unloading is required for rectification. If the angle is
too large, the wheel breaks down too quickly.
"With wheels costing
$1,100 each, the ability for them to function correctly becomes
a big factor". "The spindle angle also determines wafer
thickness uniformity, which is absolutely necessary" said
Kwilinski.
He described the long and complex operation of adjusting a grinding
machine, which takes it out of production for 3 hours and requires
the attention of highly trained personnel. The 3-hour savings for
each of the six or eight trials needed for each experiment is a
critical factor in managing Seagate’s wafer production system.
"The Zerotronics
sensors basically let us know where we're at, and this is a vital
bit of information we need to set up the grinders correctly and
to know where the wheel spindle is in space." said Kwilinski.
The wheels are 11 inches in diameter with a band of abrasive 1/8-inch
wide. Tolerance for every point on every wafer is ±8 microns. The
wafers measure 4 1/2 inches square and 1 1/4 millimeters thick.
It takes about 45 days to produce a wafer and requires more than
100 operations.
SYSTEM
BENEFITS
- Increased
efficiency of tightly controlled
and fine-tolerance processing operations.
- Complete
measurement accuracy.
- Savings
of 3 hours.
|
The device handles both
small angles with a high resolution as well as large angles. A temperature
sensor mathematically compensates for changing environmental conditions,
which improves measurement results.