Machine
shop cuts gage-setting time by 50%
"We're a production
machine shop," said Dennis Murphy, quality assurance manager at
McSwain Manufacturing, Cincinnati. The company crafts specialized
parts for industries including power generation, computers, and
aerospace, and also performs some light assembly. Components are
fashioned on such large machinery as vertical turret lathes and
horizontal boring mills, then shipped directly to McSwain's
customers for assembly into gas turbine engines and other end products.
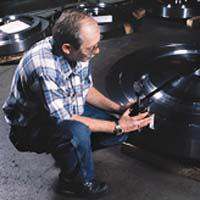
About a year ago, the
company relied on gage blocks to set the more than 60 adjustable-length
gages that measure the machined parts. This process was anything
but simple. "You start ringing those blocks together, you're
trying to hold them together, puts rods through them, dirt gets
between them, oil gets between them," explained Murphy. Whoever
set up the gage blocks then had to add up the total length, making
sure to do so carefully lest a mistake be made during calculation.
"Now all of a sudden, you're saying that I'm ten thousandths
off," said Murphy. "Well, I must have missed ten thousandths'I
better add a block that makes that up, and now all of a sudden you're
going to cut ten thousandths off."
Potential human error
was not the only source of frustration for McSwain. It often took
30 to 45 min. just to set up the gage blocks. These factors motivated
the company to look for a more accurate, faster, easier way to set
the gages. "We had to find something that made a permanent fix to
the problem," Murphy said, insistent that the company would not
accept any more gage-setting errors. That's when McSwain decided
to purchase a Trimos horizontal length setting
instrument supplied by Fred V. Fowler Co. Inc., Newton, MA.
The Swiss-made, granite-based,
80-in. device simplified the gage-setting process for McSwain by
reducing the number of calibration steps. The operator dials in
the required gage setting, locks it, and then sets the gage directly
from the Trimos. The entire process takes 10 to 15 min. The company
sets bore gages with the instrument as well. Murphy can also document
the settings, in case of a customer inquiry. "We print out what
we set [the gage] to, staple that printout to the gage request that
the operator turned in to have his gage set up, and then file that,"
he said. Should a customer question McSwain's measurement
process, the company can reference the printout.
Because of the simpler
setup and reduced setting time, fewer operators were required. With
the gage blocks, Murphy had to dedicate up to three inspectors to
work on gage setting. Since McSwain acquired the Trimos, he only
requires one inspector. Because a calculator is no longer required
for gage setup, the company has also seen incidences of operator
error drop significantly. Accuracy has improved from errors in the
range of 0.010 in. with the gage blocks to 0.00038 in. with the
Trimos. The instrument was also easy to learn. Personnel were shown
how to operate the Trimos, and able to use it in only a short time.
SYSTEM
BENEFITS
- Gage setting
time cut from 30 to 15 min.
- Number of
inspectors reduced from 3 to 1
- 10 to 1
reduction in gage-setting errors
|
McSwain has experienced
many benefits from the length-setting instrument'greater accuracy,
speed, documentation capability'and it is determined to see
that these benefits last, and prevent a reoccurrence of the old
gage-setting problems. "A lot of the times, with machine shops like
us, you're in a fire-fighting mode," explained Murphy. "You're
always reacting to problems instead of making permanent fixes. This
is an actual preventive measure that's been taken."